Detaillierte Planungsunterlagen für Fertigungsprojekte
Facility Management: Fertigung » Leistungen » Ausführungsplanung » Leistungsphase 5 der HOAI
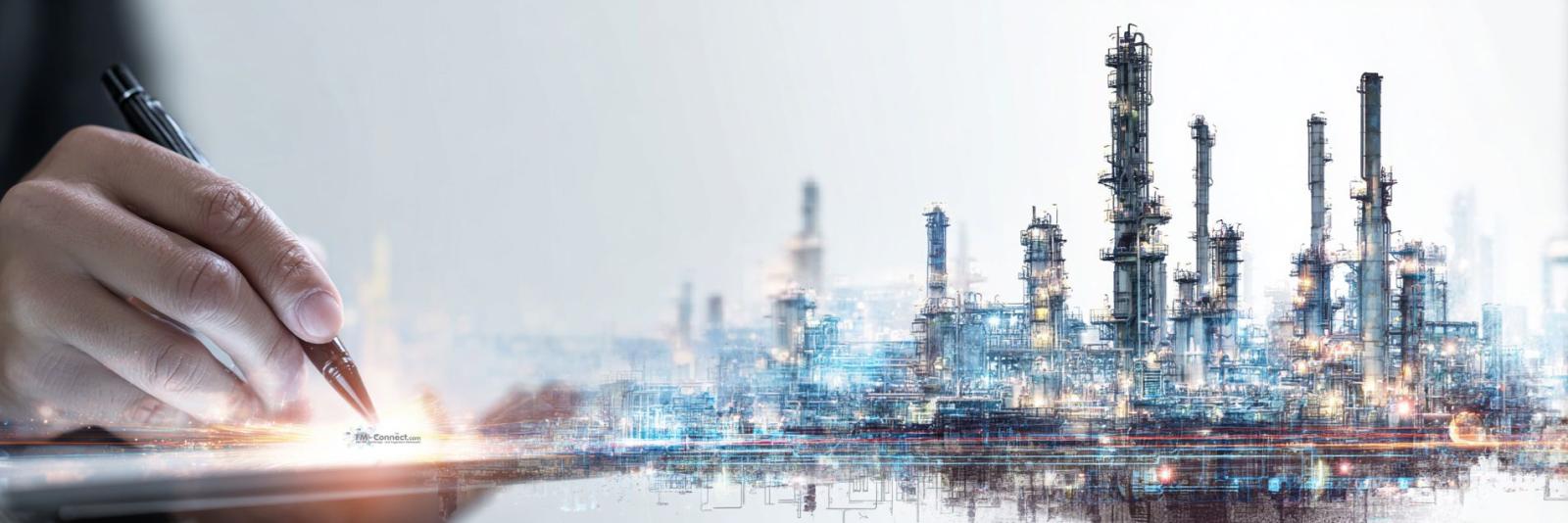
Fertigung: HOAI-Leistungsphase 5: Funktionale Anforderungen an Fertigungsstätten
Industrielle Fertigungsstätten stellen komplexe Anforderungen an Planung und Ausführung. Bereits in der Leistungsphase 5 (Ausführungsplanung) nach HOAI müssen sämtliche funktionalen Anforderungen integriert werden, um einen reibungslosen, sicheren und effizienten Betrieb zu gewährleisten. Eine durchdachte Ausführungsplanung entscheidet darüber, ob Instandhaltung, Reinigung, Versorgung und Produktion später konfliktfrei ineinandergreifen – oder ob kostspielige Nachbesserungen und Betriebsunterbrechungen drohen. Wesentliche Schwerpunkte sind die technische Infrastruktur, welche Strom, Druckluft, Wasser, IT und Entsorgung zuverlässig bereitstellt, und die Gebäudegestaltung, die ausreichend Platz, Tragfähigkeit und Medienführung für alle Maschinen und Prozesse bietet. Zugleich müssen Verkehrswege und Logistikflächen sicher und effizient organisiert werden, damit Personen- und Materialflüsse reibungslos verlaufen. Die Arbeitsumgebung – Licht, Klima, Schall, Luft – ist so zu gestalten, dass sie Gesundheit und Produktqualität fördert. Aspekte wie Instandhaltung und Reinigung dürfen nicht erst im Nachhinein bedacht werden, sondern fließen von Anfang an in die Planung ein. All diese Punkte in einem konsistenten Ausführungsplan zu vereinen, erfordert interdisziplinäre Abstimmung und vorausschauende Planung. Die Integration dieser Anforderungen in LPh 5 bedeutet konkret, dass in den Zeichnungen, Leistungsbeschreibungen und Anlagenlisten jede Forderung verortet und nachverfolgbar ist – von der exakten Position eines Revisionsschachts bis zur Benennung eines Übergabepunktes der Druckluft. Nur so kann später im Bau und Betrieb das Zusammenspiel von Gebäude und Fertigung reibungslos funktionieren. Typische Planungsfehler – mangelhafte Abstimmung, fehlende Zugänge, unterschätzte Reserven – lassen sich durch systematische Qualitätssicherungsmaßnahmen und Checklisten proaktiv vermeiden.
- Gesetzliche
- Anforderungen
- Funktionale
- Logistikzonen
- Beleuchtung
- Instandhaltung
- Integration
- Planungsfehler
- Checkliste
Gesetzliche und normative Grundlagen für Fertigungsbauten
Die Planung von Fertigungsstätten in Deutschland wird maßgeblich durch Gesetze, Verordnungen und technische Normen bestimmt. Zentrale Bedeutung hat die Verordnung über Arbeitsstätten (Arbeitsstättenverordnung, ArbStättV), die konkrete Anforderungen an Sicherheit und Gesundheitsschutz in Arbeitsstätten stellt. Sie fordert u. a., dass Arbeitsräume ausreichend bemessen, mit Tageslicht und geeigneter Beleuchtung ausgestattet und ausreichend belüftet sein müssen. Zur ArbStättV existieren detaillierte Technische Regeln für Arbeitsstätten (ASR), die den Stand der Technik präzisieren. Bei Einhaltung der ASR kann ein Arbeitgeber davon ausgehen, dass die entsprechenden Anforderungen der Verordnung erfüllt sind. So konkretisiert z. B. ASR A1.2 die erforderlichen Raummaße: Arbeitsräume bis 50 m² Grundfläche müssen mindestens 2,50 m hoch sein, bei größeren Flächen mindestens 2,75 m. Auch die notwendigen Bewegungsflächen an Arbeitsplätzen und Verkehrswege werden in ASR A1.2 festgelegt. Weitere Regeln behandeln z. B. Verkehrswege (ASR A1.8), Türen und Tore (ASR A1.7), Beleuchtung (ASR A3.4), Raumtemperatur (ASR A3.5), Lüftung (ASR A3.6) und Lärm (ASR A3.7). Die ASR spiegeln gesicherte arbeitswissenschaftliche Erkenntnisse wider und haben Vermutungswirkung hinsichtlich der ArbStättV-Erfüllung.
Ergänzend zur ArbStättV sind bauordnungsrechtliche Vorgaben zu beachten. Insbesondere die Landesbauordnungen und ggf. Sondervorschriften für Industriebauten (z. B. die Muster-Industriebau-Richtlinie) definieren bauliche Anforderungen etwa an Feuerwiderstand, Fluchtwege und statische Lastannahmen. Für die Qualität von Böden ist DIN 18202 „Toleranzen im Hochbau“ relevant. Sie legt Grenzwerte für Ebenheits- und Maßtoleranzen fest. Insbesondere Industrieböden müssen sehr eben ausgeführt sein, um z. B. den sicheren Betrieb von Flurförderzeugen und eine präzise Maschinenaufstellung zu ermöglichen. Unebenheiten oder Stolperstellen über 4 mm sind zu vermeiden. Weitere DIN-Normen betreffen z. B. die Beschaffenheit von Arbeitsböden (Rutschhemmung nach DIN 51130 für ölbelastete Bereiche), die Beleuchtung von Arbeitsstätten (DIN EN 12464-1) oder die Schallsituation (DIN 18041 für Raumakustik). Branchenspezifische Richtlinien – etwa die VDI-Richtlinienreihe 2083 für Reinräume – definieren zusätzliche Anforderungen an Spezialbereiche (z. B. Reinheitsklassen nach ISO 14644-1 für Reinräume). Insgesamt ergibt sich ein dichtes Netz an Vorschriften, das in der Planung von Fertigungsstätten eingehalten werden muss. Eine sorgfältige Analyse der gesetzlichen und normativen Grundlagen bildet daher die Basis der Ausführungsplanung.
Anforderungen an die technische Infrastruktur
Ein effizienter Fertigungsbetrieb erfordert eine leistungsfähige technische Infrastruktur.
In der Ausführungsplanung sind sämtliche Versorgungsmedien bedarfsgerecht auszulegen und klar zwischen Gebäude- und Produktionsverantwortung abzugrenzen:
Stromversorgung: Fertigungsstätten haben meist einen hohen Strombedarf durch Maschinen, Anlagen und Infrastruktur. Es sind geeignete Transformatoren, Unterverteilungen und Stromkreise zu planen, die Lastspitzen abfangen und eine selektive Abschaltung ermöglichen. Kritische Bereiche (z. B. IT-Serverräume oder Sicherheitssysteme) benötigen unter Umständen USV-Anlagen oder Notstromaggregate. Wichtig ist die Trennung von Stromkreisen für Produktion und allgemeine Infrastruktur, um gegenseitige Beeinflussungen zu vermeiden. Abschalt- und Wartungsschalter sind so anzuordnen, dass Teile der Anlage spannungsfrei geschaltet werden können, ohne die gesamte Produktion stillzulegen.
Druckluft: Viele Maschinen und Werkzeuge benötigen Druckluft. Die Druckluftversorgung ist mit ausreichender Kompressorleistung, Trocknung und Filterung auszulegen. Hauptleitungen sollten vom Gebäude gestellt werden, die Endabnahmen aber in Maschinenähe erfolgen. Übergabepunkte (z. B. Kupplungen) zwischen Gebäude-Druckluftnetz und Maschinen sind eindeutig zu definieren. Zudem empfiehlt es sich, Druckluftqualitäten gemäß ISO 8573-1 (Öl-/Partikelgehalt) festzulegen, falls sensible Prozesse das erfordern. Für Wartungsarbeiten müssen Ablass- und Entlüftungsventile vorgesehen werden.
Wasserversorgung: In Fertigungsstätten wird Wasser z. B. als Kühlwasser, Prozesswasser oder für sanitäre Anlagen benötigt. Die Planung muss den erforderlichen Wasserdruck und -durchfluss sicherstellen. Gegebenenfalls sind Ringleitungen mit Zirkulation vorzusehen (um z. B. Temperaturanforderungen einzuhalten oder Legionellenbildung zu verhindern). Bei Brauch- und Abwasser sind technische Aufbereitungsanlagen (Filter, Ölabscheider etc.) sowie Anschlüsse an die Entsorgung einzuplanen. Kühlwasser für Maschinen oder Klima-Anlagen erfordert Rückkühlwerke oder Kühltürme mit ausreichenden Kapazitäten. Auch technische Gase (Druckgase wie Stickstoff, Schweißgase etc.) müssen bei Bedarf über fest installierte Leitungen bis zu den Verbrauchsstellen geführt und mit Absperreinrichtungen ausgestattet werden.
IT und Netzwerk: Die Digitalisierung (Stichwort Industrie 4.0) macht eine hochverfügbare IT-Infrastruktur unabdingbar. Bereits in der Ausführungsplanung sind Datenkabel-Trassen, Serverräume und Anschlusspunkte für Maschinen zu berücksichtigen. Es empfiehlt sich eine strukturierte Verkabelung mit Reserven (z. B. Leerrohre oder Kabelbahnen mit Reserveflächen für zusätzliche Kabel). Besonders in automatisierten Anlagen müssen Netzwerke echtzeitfähig und redundant ausgelegt sein. WLAN-Abdeckung für mobile Geräte oder fahrerlose Transportsysteme ist zu prüfen. Sicherheitstechnische Anlagen (Zutrittskontrolle, CCTV, Brandmeldeanlagen) erfordern ebenfalls IT-Verkabelung, oft getrennt vom Produktionsnetz.
Entsorgung und Abfallmanagement: Fertigungsprozesse erzeugen Abfälle und Reststoffe, deren Handhabung in der Planung berücksichtigt sein muss. Dies umfasst Müllsammelstellen, Containerstellplätze und interne Transportwege für Abfälle. Für gefährliche Abfälle (z. B. Chemikalien, ölhaltige Stoffe) sind geeignete Lagerbereiche nach Gefahrstoffrecht (z. B. Auffangwannen, Belüftung) vorzusehen. Rohrpost- oder Vakuum-Fördersysteme können die Entsorgung kleiner Teile oder Stäube automatisieren. Ferner sind Anschlüsse für Entsorgungsbetriebe (z. B. Presscontainer mit LKW-Zufahrt) einzuplanen. Insgesamt muss die Infrastruktur so gestaltet sein, dass Medien trennscharf übergeben werden – die Verantwortlichkeiten zwischen Gebäude-FM und Produktionstechnik sollen an definierten Schnittstellen liegen. Reserven und Erweiterungsmöglichkeiten (zusätzliche Kabelzüge, freie Sicherungsplätze, Rohrleitungsreserven) sind einzuplanen, um künftige Anpassungen zu erleichtern
Funktionale Anforderungen an Gebäude und Anlagenlayout
Die bauliche Gestaltung der Fertigungsstätte muss die Produktionsprozesse optimal unterstützen.
Raumabmessungen, Medienführung, Wartungszonen und Maschinenaufstellungen sind so zu planen, dass sie den betrieblichen Anforderungen genügen und zugleich den gesetzlichen Vorgaben entsprechen.
Raumhöhen und Hallengeometrie: Fertigungshallen erfordern oft großzügige lichte Höhen. Gesetzlich sind gemäß ASR A1.2 mindestens 2,75 m bei Arbeitsräumen über 50 m² Grundfläche vorgeschrieben. In der Praxis liegen Hallenhöhen meist deutlich höher (6 m und mehr), um z. B. Kragarmregale, Brückenkrane oder hohe Maschinen unterzubringen. Die Ausführungsplanung muss neben der Mindesthöhe auch Kranbahnen, Hängeförderer oder Lüftungskanäle berücksichtigen, die unter der Decke verlaufen. Stützen und Binder sind so anzuordnen, dass sie die Produktionsfläche möglichst wenig einschränken (große Stützweiten, Hallen in Skelettbauweise). Zwischenebenen oder Bühnen für Technik (z. B. Lüftungszentralen) können genutzt werden, sofern die Höhenplanung dies zulässt. Wichtig ist, dass ausreichend Abstand zwischen Technikdecken und Produktionsbereich bleibt, damit Filterwechsel, Wartung der Beleuchtung etc. über Podeste oder Hebebühnen möglich sind. Für Reinräume gelten zusätzlich spezielle Deckensysteme mit Laminar-Flow-Elementen, die meist abgehängte Filtermodule erfordern – was extra Deckenhöhe beansprucht.
Bodenbeschaffenheit: Der Industrieboden muss extrem belastbar, eben und rutschfest sein. Für schwere Maschinen und Regale sind Bodenlasten nach Nutzung anzusetzen (häufig 5–10 kN/m² oder mehr, je nach Maschinengewicht). Punktlasten (z. B. von Maschinenfüßen oder Staplerreifen) sind über geeignete Fundamente oder verstärkte Bodenplatten abzufangen. Die Ebenheit des Bodens richtet sich nach DIN 18202. In Produktions- und Lagerbereichen ist mindestens die Ebenheitsklasse der DIN 18202, Tabelle 3, Zeile 3 einzuhalten. Das bedeutet z. B., dass bei einer Messstrecke von 2 m keine Höhenabweichung über ~3 mm auftreten darf. Höherwertige Ebenheiten sind für bestimmte Fälle (etwa Schmalgang-Hochregallager) erforderlich. Unebenheiten >4 mm gelten bereits als Stolperstelle. Zudem muss der Boden je nach Nutzung rutschhemmend ausgeführt sein (z. B. Oberfläche mit R11/R12 nach BGR 181 für ölverschmierte Bereiche). In Nassbereichen sind Bodenabläufe mit Gefälle (ca. 1–2%) vorzusehen, um Reinigungsflüssigkeiten aufzunehmen. Die Auswahl des Bodenbelags (Stahlfaserbeton, Hartstoffschicht, Epoxidharzbeschichtung etc.) sollte die mechanischen und chemischen Beanspruchungen berücksichtigen. Beschichtungen können auch zur Staubbindung und leichteren Reinigung dienen – im Reinraum sind z. B. ableitfähige, porenfreie Beläge Pflicht.
Medienführung und Versorgung im Hallenlayout: Die Verteilung von Medien (Stromkabel, Druckluft-, Wasser- und Datenleitungen) innerhalb der Halle erfordert eine durchdachte Trassenplanung. Häufig werden Medientrassen oberhalb der Fertigungszonen an Kabeltragsystemen, Laufstegen oder abgehängten Schienen geführt. Dies hält den Boden frei von Leitungen und erleichtert Anpassungen. In der Ausführungsplanung sind ausreichend Trassenreserven einzuplanen – also Platz auf Kabeltrassen und Rohrhalterungen für später nachrüstbare Leitungen. Wo Medien vom Boden aus benötigt werden (z. B. Energiezufuhr für Maschinen in Insellage), können Bodentanks, Unterflurkanäle oder Steigeböcke vorgesehen werden. Wichtig ist, dass Versorgungsleitungen keine Arbeitswege kreuzen oder Stolperfallen bilden; sofern unvermeidbar, sind Kabelbrücken oder Markierungen anzubringen. Medieninseln oder Deckenschienen mit absenkbaren Anschlüssen (Drops) ermöglichen flexible Maschinenaufstellungen. In Reinräumen müssen Medienführungen besonders dicht und leicht zu reinigen sein (glatte Kanaloberflächen, minimale Partikelbildung). Die Schnittstellen zwischen Gebäude und Maschine sind exakt zu definieren: Beispielsweise endet die bauseitige Druckluftleitung an einem Kugelhahn mit definierter Kupplung, an die der Maschinenhersteller anschließt. Solche Übergabepunkte sind in Plänen darzustellen, um Verantwortlichkeiten zu klären.
Wartungszonen und Zugänglichkeit: Ein häufig unterschätzter Aspekt ist die Zugänglichkeit von Anlagen für Wartung und Instandhaltung. Technikräume (z. B. für Elektro, Heizung, Lüftung) müssen ausreichend Platz bieten, damit Wartungsarbeiten ergonomisch durchgeführt werden können. Es sind Wartungsgassen und Bedienflächen vor Schaltanlagen, Kessel etc. einzuplanen (typisch sind 0,8–1,2 m Freiraum, je nach Vorschrift der Berufsgenossenschaft). Auch im Produktionsbereich dürfen Maschinen nicht so eng stehen, dass notwendige Revisionsarbeiten behindert werden. Revisionsklappen und -öffnungen in Schächten, abgehängten Decken oder Kanälen sind vorzusehen, um z. B. Absperrarmaturen, Sensoren und Filter zugänglich zu halten. Insbesondere Versorgungsleitungen sollten so verlegt sein, dass Bauteile (Ventile, Messgeräte) erreichbar sind, ohne die Produktion großflächig zu demontieren. ASR A1.8 fordert für Gänge zur Instandhaltung eine Mindestbreite von 0,60 m und eine Höhe von 1,90 m. Dies gilt etwa für Durchgänge hinter Maschinen oder Steigleitern zu Podesten. Solche Instandhaltungsgänge sind in den Planunterlagen kenntlich zu machen. Zur Wartungsfreundlichkeit gehört auch, Maschinen so anzuordnen, dass sie im Bedarfsfall freigegeben und abgeschaltet werden können, ohne Kaskadeneffekte auf andere Anlagenteile. Wo Maschinen mit Schutzgittern oder Einhausungen versehen sind, sollten ausreichende Serviceöffnungen vorhanden sein, die idealerweise verriegelt sind (Zugang nur für befugtes Personal). All diese Aspekte – von Zugangsluken über Laufstege bis zu Anschlagpunkten für Hebezeuge – müssen integraler Bestandteil der Ausführungsplanung sein, um einen späteren reibungslosen Betrieb zu ermöglichen.
Maschinenaufstellung und Fundamentierung: Die Positionierung der Maschinen in der Halle bestimmt die Produktionsabläufe wesentlich. Schon in Phase 5 werden Maschinenlayouts oft in Abstimmung mit Anlagenlieferanten verfeinert. Funktionale Anforderungen sind etwa: ausreichende Abstände zwischen Maschinen, damit Bediener und Materialtransport Platz finden (typisch mind. 0,8 m zwischen größeren Anlagen, mehr bei gegenüberliegenden Arbeitsplätzen). Sicherheitsabstände gemäß Maschinenrichtlinie (z. B. Gefahrenbereich Absperrungen nach EN ISO 13857) müssen berücksichtigt werden. Schwere oder schwingende Maschinen (Pressen, Stanzen, große Fräsen) erfordern häufig eigene Fundamentblöcke entkoppelt vom Hallenboden, um Vibrationen zu isolieren. Die Ausführungsplanung muss hier enge Toleranzen einhalten (Fundamentebene, Lage der Ankerschrauben) – oft geben Maschinenhersteller genaue Pläne vor. Zudem sind Schwingungsdämpfer oder elastische Lager vorzusehen, damit angrenzende sensible Anlagen (Messtechnik, Präzisionsmaschinen) nicht gestört werden. Bei wärmeerzeugenden Anlagen (Öfen, Schmieden) ist die Abwärme abzuführen, z. B. durch Kühlleitungen oder Abzüge, um das Raumklima nicht zu beeinträchtigen. Materialfluss ist ein weiterer Punkt: Maschinen sollten gemäß Produktionssequenz angeordnet werden, um unnötige Transportwege zu vermeiden. Dabei müssen Zu- und Abführbänder, Roboterarbeitsbereiche und Pufferflächen mitgeplant werden. Freiräume für eventuelle Kapazitätserweiterungen (Platzhalter für zusätzliche Maschinenmodule) sind – wo absehbar – sinnvoll.
Verkehrs- und Logistikzonen innerhalb der Produktionshalle
Eine effiziente Fertigung erfordert durchdachte Verkehrs- und Logistikflächen. In Produktionshallen sind unterschiedliche Verkehrswege zu organisieren: für Personen (Mitarbeiter, Besucher), für innerbetriebliche Transporte (z. B. Gabelstapler, Routenzüge, fahrerlose Transportsysteme) und ggf. für Wartungs- und Notfälle.
Diese Wege müssen klar definiert, ausreichend dimensioniert und sicher gestaltet sein:
Fußgängerwege: Gehwege für Beschäftigte innerhalb der Fertigung sind möglichst von Fahrzeugwegen zu trennen. Markierungen am Hallenboden (gelbe Linien) und Schilder gemäß ASR A1.3 kennzeichnen die Laufwege und Bereiche, die nicht betreten werden dürfen. Die Breite der Gehwege richtet sich nach der Personenanzahl: Bis 5 Personen genügen 0,9 m, bei mehr Personen sind 1,2 m oder mehr erforderlich. Hauptwege, die auch als Fluchtwege dienen, müssen mindestens 1,2 m breit sein (bzw. 0,90 m Durchgangsbreite durch Türen). An Engstellen oder Türen dürfen die Mindestbreiten nur kurzzeitig unterschritten werden. Die lichte Höhe über Gehwegen soll 2,10 m betragen und darf nicht unter 2,00 m sinken – vorspringende Bauteile oder abgehängte Installationen müssen also außerhalb der Durchgangshöhe liegen bzw. gepolstert und markiert werden.
Fahrwege für Flurförderzeuge: In vielen Fertigungsstätten gehören Gabelstapler, Hubwagen oder Routenzüge zum täglichen Bild. Deren Fahrwege sind so anzulegen, dass sie ausreichend breit sind und Kurvenradien ermöglichen. Die Mindestbreite eines reinen Staplerfahrwegs ergibt sich aus der Fahrzeugbreite plus beidseitigem Sicherheitsabstand (meist je 0,5 m). Führen Staplerwege an Türen, Durchgängen oder Treppen vorbei, ist ein Abstand von 1,0 m einzuhalten. Idealerweise werden Fuß- und Staplerverkehr vollständig getrennt – z. B. durch Geländer oder Barrieren in stark frequentierten Bereichen (etwa entlang von Produktionslinien). Kreuzungsbereiche können mit optischen oder akustischen Warnsystemen (Spiegelsysteme, Blinklampen bei Annäherung) gesichert werden. Richtungsverkehr (Einbahnverkehr) für Stapler reduziert das Unfallrisiko in engen Gängen. Ferner sind ausreichend Wendeflächen einzuplanen: Ein Gabelstapler benötigt je nach Typ einen Wenderadius von 2–3 m; an Enden von Gängen sollte eine Aufweitung vorhanden sein, damit Fahrzeuge sicher drehen können. Auch Überholstellen bzw. Begegnungsbuchten sind vorzusehen, wenn zweirichtungs Verkehr nicht ausgeschlossen ist – hier empfiehlt ASR A1.8 zusätzliche Breite oder Einblick über Spiegel, damit sich stapler begegnen können.
Lager- und Pufferflächen: Neben den reinen Verkehrswegen müssen Flächen für Material bereitgestellt werden. Warenannahme und Versand erfordern Fläche für LKW-Zufahrt, Andockrampen, ggf. Schleusen (z. B. bei gekühlten Bereichen oder Reinräumen). Lagerzonen innerhalb der Halle – seien es Rohmaterial, Zwischenlager oder Fertigwarenpuffer – sind so anzuordnen, dass sie den Materialfluss nicht behindern. Regalreihen sollten im 90°-Winkel zum Haupttransportweg ausgerichtet sein, um ein zügiges Ein- und Auslagern zu ermöglichen. Für Staplerlager gilt es, gemäß BG-Regeln ausreichend Platz vor Regalen (mind. 1,5 facher Regalhöhenabstand bei frontaler Bedienung) und Sicherheitsabstände zu Wänden einzuhalten. Ladezonen für Routenzüge oder die Bereitstellung von Materialkisten an der Linie („Supermärkte“) müssen ebenfalls als Flächen eingeplant und mit geeigneten Bodenmarkierungen gekennzeichnet werden.
Interne Logistik und Layout: Die Anordnung von Arbeitsplätzen und Stationen sollte einem logischen Produktionsfluss folgen, um unnötige Transporte zu vermeiden. Wo Fließfertigung besteht, müssen Fördereinrichtungen (z. B. Rollbänder, Skid-Systeme, AGV-Routen) exakt in die Hallenplanung integriert werden. Leitlinien für fahrerlose Transportsysteme können aufgemalt oder induktiv im Boden verlegt sein – die Planungsdokumente sollten solche Führungssysteme früh berücksichtigen, da sie spezielle Anforderungen an den Boden (Ebenheit, Magnetstreifen) stellen. Darüber hinaus sind Nebenwege einzuplanen: etwa für Reinigungspersonal, das mit Reinigungsmaschinen durch die Halle fährt, oder für Instandhalter, die mit Werkzeugwagen an die Anlagen gelangen. Um Konflikte zwischen verschiedenen Verkehrsarten zu minimieren, empfiehlt es sich, Zonen festzulegen (z. B. Materialzone, Personen-Zone) und diese baulich oder organisatorisch zu trennen. Beispiele sind erhöhte Gehwege oder Schutzgeländer entlang von Hauptgehwegen. Auch PSA-Zonen (Bereiche mit Pflicht zum Tragen Persönlicher Schutzausrüstung, etwa Gehörschutz oder Atemschutz) sollten bereits räumlich eingegrenzt und ausgeschildert sein. Schließlich müssen Flucht- und Rettungswege absolut freigehalten werden: Die Anordnung von Maschinen und Regalen darf Notausgänge nicht versperren, und es sind ausreichend viele, möglichst direkte Fluchtwege entsprechend ASR A2.3 aus jeder Hallenposition zu gewährleisten. Summiert man alle Anforderungen, zeigt sich, dass Verkehrs- und Logistikkonzepte integraler Bestandteil einer ganzheitlichen Ausführungsplanung sind – Sicherheitsaspekte, Effizienz und Ergonomie gehen hier Hand in Hand.
Anforderungen an Beleuchtung, Raumklima, Schallschutz und Belüftung
Die Arbeitsumgebungsbedingungen in einer Fertigungsstätte beeinflussen nicht nur das Wohlbefinden der Beschäftigten, sondern auch die Produktqualität und Prozesssicherheit.
Daher müssen Beleuchtung, Klima, Lärm und Lüftung mit Sorgfalt geplant werden:
Beleuchtung: Eine ausreichende und blendfreie Beleuchtung ist in Produktionsbereichen unverzichtbar. Die ArbStättV fordert möglichst viel Tageslicht und eine dem Arbeitsschutz angemessene künstliche Beleuchtung. Große Fensterflächen, Oberlichter oder Lichtbänder im Dach tragen dazu bei, Tageslicht einzubringen – was nicht nur die Sehbedingungen verbessert, sondern auch Energie spart. Zugleich muss direkte Blendung oder zu starke Sonneneinstrahlung (Wärmeeintrag) vermieden werden, etwa durch Sonnenschutzverglasung oder Jalousien. Künstliches Licht wird nach ASR A3.4 so bemessen, dass Mindestbeleuchtungsstärken für die jeweiligen Sehaufgaben eingehalten werden. In normalen Montage- und Prüftätigkeiten sind oft 300–500 Lux gefordert, für Feinarbeiten (z. B. Elektronikmontage) sogar 1000 Lux und mehr. Genaue Werte listet Anhang 1 der ASR A3.4 nach Tätigkeiten auf. Wichtig ist, dass diese Werte als mittlere Beleuchtungsstärke dauerhaft erreicht werden – also eine entsprechende Lampenanordnung und Leuchtenauswahl erfolgt. Die Beleuchtungskörper sollten so platziert werden, dass Schattenwurf und Blendung minimiert werden (indirekte Beleuchtung, Diffusoren, geeignete Anstrahlwinkel). In hohen Hallen kommen häufig Pendelleuchten oder LED-Highbays zum Einsatz; deren Wartungsfreundlichkeit (Leuchtmittelwechsel) ist mitzudenken – z. B. via Schienensysteme, an denen Leuchten in Wartungsposition gefahren werden können. Zudem ist Notbeleuchtung gemäß ASR A3.4/7 vorzusehen: Im Notfall (Stromausfall) müssen Fluchtwege mit mindestens 1 Lux beleuchtet sein und Sicherheitsleuchten deutlich erkennbar sein. Prüfgeräte oder Qualitätskontrollbereiche benötigen eventuell spezielle Farbwiedergabeleuchten (Ra-Index ≥ 90), um Farbabweichungen erkennen zu können (z. B. in der Lackiererei oder Textilproduktion). All diese Beleuchtungsanforderungen sind bereits in der Ausführungsplanung zu verankern, da sie Einfluss auf die Elektroinstallation (Kabeltrassen, Schaltkreise, Notstrom) und die Gebäudegeometrie (z. B. Position von Oberlichtern) haben.
Raumklima (Temperatur, Luftfeuchte): Das Innenraumklima in Fertigungsbereichen unterliegt je nach Tätigkeit bestimmten Richtwerten. Gemäß ASR A3.5 müssen in Arbeitsräumen gesundheitlich zuträgliche Temperaturen herrschen. Konkret nennt die ASR A3.5 als Untergrenzen: mindestens +20 °C für leichte sitzende Tätigkeiten, +17 °C für mittelschwere Tätigkeiten im Stehen/Gehen und +12 °C für schwere körperliche Arbeit. Diese Mindesttemperaturen sind durch Heizung sicherzustellen, sofern die Außentemperaturen niedriger sind. In großen Hallen erfolgt die Beheizung oft über Deckenstrahler, Warmluftgebläse oder Fußbodenheizungen (letzteres in Werkstätten beliebt, aber bei Hallenneubauten wegen großer Fläche weniger effizient). Gleichzeitig darf die Temperatur nicht übermäßig hoch steigen: Bei Bürotätigkeit liegt der empfohlene Maximalwert bei 26 °C; in Produktionshallen ohne Klimatisierung können im Sommer höhere Werte auftreten, doch ab 30 °C Raumtemperatur sind vom Arbeitgeber Maßnahmen zu ergreifen (Sonnenschutz, Lüftung, Trinkangebote). Eine Kühlung von Fertigungshallen ist aus Energiegründen selten flächendeckend, aber bei temperaturempfindlichen Prozessen (Elektronikfertigung, Pharmaproduktion) oder Reinräumen unerlässlich. Hier kommen Kaltwasserkühlanlagen oder Klimageräte zum Einsatz, deren Dimensionierung Teil der TGA-Planung in LPh 5 ist. Ferner ist die Luftfeuchtigkeit zu beachten: Sie sollte meist im Bereich 40–60% liegen, um ein angenehmes und für Materialien zuträgliches Klima zu schaffen. In ESD-geschützten Bereichen (Elektronik) oder bei Holz/Lack kann eine bestimmte Feuchtehaltung nötig sein, was Befeuchter oder Trockner erfordert. Zugluft ist zu vermeiden – ASR A3.6 betont, dass keine störenden Luftzüge auf die Beschäftigten einwirken dürfen. Dies ist insbesondere bei toröffnungen im Winter oder starken Hallenlüftungsanlagen relevant; planerisch kann man z. B. Luftschleieranlagen an Toren und eine sorgfältige Auslegung der Lüftungsgitter vorsehen.
Lärmschutz und akustische Bedingungen: In industriellen Anlagen treten vielfältige Lärmquellen auf – Maschinenlärm, Druckluftabblasungen, Ventilatoren, Transporte etc.. Der Arbeitsschutz fordert, dass die Lärmbelastung der Beschäftigten so gering wie möglich gehalten wird. Nach der Lärm- und Vibrations-Arbeitsschutzverordnung (LärmVibrationsArbSchV) liegt der obere Auslösewert für Lärm bei 85 dB(A) Tages-Lärmexpositionspegel; ab diesem Wert müssen Gehörschutz bereitgestellt und getragen werden. Die Planung sollte darauf abzielen, bauliche und technische Lärmminderungsmaßnahmen umzusetzen, damit im Dauerbetrieb möglichst keine Arbeitsplätze diesen Wert überschreiten. Dazu zählen z. B. akustische Abschirmungen: laute Anlagen wie Kompressoren oder Hydraulikaggregate werden in separate Technikräume verbannt, die schallgedämmt sind. Auch Schallschutzhauben oder Kapselungen an Maschinen sind vorzusehen, soweit mit Herstellern umsetzbar. Hallenwände und -decken können mit schallabsorbierenden Materialien (z. B. Akustikpaneele, Baffeln) ausgestattet werden, um den Nachhall zu reduzieren – dies verbessert die Verständigung und vermindert die Lärmsumme im Raum. Normen wie DIN 18041 geben hierzu Auslegungsgrößen für die Raumakustik vor. Gleichzeitig muss die Kommunikationsfähigkeit erhalten bleiben: In Bereichen, wo Mitarbeiter verbal kommunizieren oder akustische Signale hören müssen (z. B. Montageband mit Teamabstimmung, Warnsignale von Staplern), darf der Hintergrundlärm nicht zu hoch sein. Es empfiehlt sich, Zonen mit unterschiedlichem Lärmpegel zu planen – etwa Ruhige Zonen für Büros oder Pausenräume in der Produktion abzuschirmen (durch Bauteile mit hohem Schalldämm-Maß). Schwingungen und Erschütterungen, die sich in Körperschall wandeln, gilt es ebenfalls zu beachten: Pumpen und Lüftungsanlagen sollten auf schwingungsentkoppelten Lagern montiert werden. In Summe entsteht ein Akustikkonzept, das Maschinenlärm und infrastrukturelle Geräusche gemeinsam behandelt. Dieses sollte sich an einschlägigen Richtlinien orientieren, z. B. VDI 2058 (Beurteilung von Lärmeinwirkungen) und VDI 2081 (Lärmminderung in Lüftungsanlagen), sowie die Einhaltung der ASR A3.7 „Lärm“ sicherstellen.
Lüftung und Luftqualität: Eine ausreichende Belüftung ist für Gesundheit und Prozessstabilität notwendig. Die ArbStättV fordert in Anhang 3.6, dass ausreichend gesundheitlich zuträgliche Atemluft in Arbeitsräumen vorhanden sein muss. In der Ausführungsplanung ist daher ein Lüftungskonzept zu erarbeiten. Für viele Hallen genügt eine freie Lüftung über natürliche Fenster- und Türöffnungen nicht, insbesondere wenn Emissionen oder große Wärmelasten anfallen. Meist wird eine mechanische Lüftungsanlage (RLT-Anlage) erforderlich, die den Luftaustausch sicherstellt. Diese ist anhand der Personenbelegung, der Raumgröße und der Prozessabluft auszulegen. Die ASR A3.6 enthält Berechnungsgrundlagen, z. B. empfohlene Außenluftvolumenströme pro Person. Ein Richtwert ist häufig 30 m³/h Frischluft pro Person, variiert aber je nach Tätigkeit und evtl. vorhandenen Schadstoffquellen. Werden z. B. Schweißarbeiten oder Lösemittelanwendungen durchgeführt, müssen Absauganlagen an den Entstehungsorten (Punktabsaugung nach Gefahrstoffverordnung) integriert werden. Die abgesaugte Luft ist ggf. über Filter (Aktivkohle, Partikelfilter) zu reinigen, bevor sie ins Freie entlassen wird. Die Zuluftführung sollte zugluftfrei und möglichst von oben nach unten erfolgen (Verdrängungslüftung), um kontaminierte Luft aus dem Aufenthaltsbereich der Beschäftigten herauszuführen. Bei Reinräumen gelten besonders strenge Regeln: Luftreinheitsklassen gemäß ISO 14644-1 definieren maximale Partikelzahlen, die nur durch Hochleistungsfilter (HEPA) und hohe Luftwechselraten erreicht werden. Reinräume haben oft Luftwechselraten von 20–600 fach pro Stunde je nach Klasse und turbulenzarme Verdrängungsströmung (Laminarflow-Decken). Die RLT-Anlagen dafür sind in separaten Technikräumen vorzusehen und müssen höchsten Hygieneansprüchen (VDI 6022, DIN 1946) genügen. Generell muss die Lüftungsanlage auch auf Wärmelasten der Maschinen reagieren: In einer Halle mit vielen Motoren oder Öfen kann erhebliche Abwärme entstehen, die abgeführt werden muss, um das Raumklima im zulässigen Bereich zu halten. Die Ausführungsunterlagen (Pläne, Schemata) sollen alle Lüftungsinstallationen umfassen, einschließlich der Lage von Lüftungsgeräten, Kanälen, Auslässen, Messstellen und Brandschutzklappen. Außerdem sind Maßnahmen für Störfälle festzuhalten: Bei Ausfall der Lüftung müssen z. B. über Fenster oder Notventilatoren alternative Lüftungsmöglichkeiten bestehen. Ein umfassendes Lüftungskonzept in LPh 5 stellt sicher, dass während des Betriebs ausreichende Luftqualität und thermischer Komfort herrschen, was nicht nur gesetzliche Pflicht, sondern auch Vorbedingung für stabile Produktionsbedingungen ist.
Instandhaltung, Reinigung und Flexibilität der Nutzung
Über den reinen Neubau hinaus muss eine Fertigungsstätte über ihren Lebenszyklus hinweg wartbar, sauber zu halten und anpassungsfähig sein.
Daher sind Aspekte der Instandhaltung und Reinigung bereits in der Ausführungsplanung mitzudenken, ebenso wie zukünftige Nutzungsänderungen oder Erweiterungen (Flexibilität):
Instandhaltungskonzept: Schon bei der Detailplanung (HOAI LPh 5) sollte ein Instandhaltungskonzept vorliegen, das festlegt, welche Intervalle und Prozeduren für Wartungen gelten und welche räumlichen Voraussetzungen dafür gebraucht werden. Die Planer müssen sicherstellen, dass es Serviceflächen gibt – z. B. genügend Platz, um Bauteile auszubauen oder Werkzeuge abzustellen. Maschinenhersteller geben oft Wartungszonen vor (etwa einen Bereich, der für den Tausch eines Motors frei sein muss). Solche Zonen sollten in den Plänen schraffiert dargestellt und bei der Aufstellung freigehalten werden. Auch Kranösen oder Anschlagpunkte in Decken, um schwere Teile zu heben, sind sinnvoll einzuplanen. Für gebäudetechnische Anlagen gilt: Filter, Pumpen, Ventilatoren etc. müssen zugänglich und austauschbar sein, ohne dass z. B. Wände aufgestemmt werden. Daher sind Revisionsöffnungen sowie demontierbare Verkleidungen vorzusehen. Die Koordination mit dem Facility Management spielt hierbei eine große Rolle: In Ausführungsplänen sollte eine Verantwortlichkeitsmatrix dokumentiert werden, wer (Gebäude-FM vs. Produktionstechnik) für welches Anlagenteil die Wartung übernimmt. Wichtig ist außerdem die zeitliche Komponente: Wartung lässt sich selten während laufender Produktion durchführen. Konzepte für Wartungsfenster (z. B. Wochenenden, Betriebsferien) sollten schon in der Planung berücksichtigt werden. Beispielsweise kann es notwendig sein, Absperrschieber oder Bypass-Leitungen einzuplanen, um Teilbereiche warten zu können, während der Rest weiterläuft. Sind regelmäßige Inspektionen durch Behörden erforderlich (z. B. TÜV-Prüfung von Druckbehältern, Brandschutzklappen), so sollten auch hierfür entsprechende Zugänge und ggf. Prüfeinrichtungen vorhanden sein (Druckmessstutzen etc.). Letztlich zielt eine wartungsfreundliche Planung darauf ab, Stillstandszeiten zu minimieren und die technische Verfügbarkeit hoch zu halten.
Reinigung und Hygiene: Die Sauberkeit von Fertigungsbereichen ist sowohl für die Produktqualität (z. B. Vermeidung von Staub in sensibler Elektronik) als auch für Arbeitssicherheit (Ölfilm = Rutschgefahr) wichtig. Die Ausführungsplanung sollte daher ein Reinigungskonzept einbeziehen. Dies betrifft zunächst die Baustoffe und Oberflächen: Wände und Böden sollen glatt, nicht staubbindend und leicht zu reinigen sein. In stark verschmutzten Bereichen (etwa Schmiede, Gießereien) sind robuste, mechanisch reinigbare Oberflächen (z. B. Stahlblechverkleidungen, geflieste Sockel) vorzusehen. Zonierung: Häufig werden Fertigungsbereiche in Sauberkeitszonen eingeteilt – z. B. ein reinraumartiger Montagebereich im Zentrum und ein umlaufender Technikgang mit höherer Schmutzbelastung. Schleusensysteme (Personalschleusen, Materialschleusen) können erforderlich sein, um zwischen Zonen zu wechseln, was räumlich in der Planung vorgesehen sein muss. Entsprechende Reinraumklassen oder Sauberkeitsstufen definieren u. a. Partikelgrenzwerte und erlaubte Materialien. Die Lüftungstechnik (Filterstufen) und die Kleidungsvorschriften der Mitarbeiter richten sich danach. Reinigungsfreundliche Konstruktion bedeutet auch: Möglichst keine unnötigen Vorsprünge, Sockel oder Kabelkanäle am Boden, wo sich Schmutz ansammelt. Rohrleitungen und Kabeltrassen sollten idealerweise von unten nach oben und nicht horizontal an Wänden verlaufen, damit sich Staub nicht oben absetzt oder sie gut abwischbar sind. Bodenabläufe und Schlitzrinnen sind dort vorzusehen, wo Flüssigkeiten anfallen oder Nassreinigung durchgeführt wird. In Lebensmittel- oder Pharmafertigungen sind z. B. Bodenrinnen aus Edelstahl mit leichtem Gefälle und Reinigungsöffnungen Standard. Zudem sollte bedacht werden, wie Reinigungsequipment in die Halle gelangt: Große Reinigungsmaschinen brauchen ausreichend breite Türen und Wege; Deckenbefahranlagen (für hohe Fenster oder Kräne) könnten eingeplant werden. Reinigungslogistik umfasst auch zentrale Orte für Reinigungsgeräte, Putzmittel und Wasseranschlüsse – solche Reinigungsräume oder Putzmittelstationen sollten in sinnvoller Nähe zu den Produktionsflächen liegen (ggf. verdeckt unter einer Treppe oder in einer Nische, aber zugänglich). Insgesamt trägt eine gut geplante Reinigungstechnik dazu bei, gleichbleibende Produktqualität und Arbeitssicherheit zu gewährleisten.
Flexibilität und Umbaufähigkeit: Industrielle Produktionsstätten unterliegen häufig Änderungen – sei es durch Produktwechsel, neue Maschinen oder Erweiterungen. Die Flexibilität der baulichen Struktur ist daher ein ökonomischer Vorteil. In der Ausführungsplanung können diverse Maßnahmen vorgesehen werden, um künftige Umbauten zu erleichtern: Beispielsweise modulare Trennwandsysteme statt massivem Mauerwerk für Büros oder Messräume innerhalb der Halle, sodass diese leicht versetzt oder entfernt werden können. Trassenreserven wurden bereits erwähnt – sie gelten als Reservekapazitäten in Kabelbahnen und Rohrleitungen, um zusätzliche Verbraucher anzuschließen. Weiterhin sind Modultrennstellen sinnvoll: An gewissen Punkten werden Anschlüsse konzentriert, wo ein neuer Hallenabschnitt oder eine zusätzliche Maschine andocken könnte, ohne das ganze Netz stillzulegen. Zum Beispiel könnte man alle Versorgungsleitungen an einer Hallenstütze mit Kupplungen versehen – hier ließe sich später ein Erweiterungsbau anschließen. Im Hallenboden können Fundamentvorsorgen (dickere Bodenplattenfelder) vorgesehen werden, wo eventuell schwere Maschinen aufgestellt werden könnten, die heute noch nicht beschafft sind. Gebäudeerweiterungen (z. B. Anbau einer weiteren Halle) sollten statisch und bauordnerisch vorbereitet sein: Entsprechende Aussteifungen, Fugen und Brandschutzmaßnahmen an Gebäudeenden ermöglichen ein Andocken neuer Baukörper mit minimalem Aufwand. Auch Erweiterungsmöglichkeiten für Sozialräume, Kantine, technische Zentralen sind zu bedenken – ein Fertigungsbetrieb wächst oft in der Belegschaft, sodass Reserveflächen oder Ausbaureserven (z. B. Rohbau für späteren Büroeinbau auf einem Zwischenmezzanin) von großem Vorteil sind. In Bezug auf Anlagentechnik kann Flexibilität durch schnell trennbare Verbindungen erreicht werden: Steckkupplungen für Elektrik und Medien an Maschinen erleichtern eine Umstellung der Anlage. Idealerweise fließen solche Anforderungen bereits in die Beschaffung der Maschinen ein (Standardisierung von Schnittstellen). Eine hohe Flexibilität spiegelt sich letztlich in der Lebenszyklusplanung wider: Das Gebäude kann neue Prozesse aufnehmen, ohne umfassende Umbauten, und damit länger genutzt werden. Dies schont Investitionsmittel und Ressourcen. Die Ausführungsplanung sollte daher nicht nur den Status quo abbilden, sondern bewusst Optionen für die Zukunft offenhalten – im Dialog mit dem Bauherrn und den Produktionsstrategen.
Integration der Anforderungen in die Ausführungsplanung (HOAI Leistungsphase 5)
Die Leistungsphase 5 nach HOAI – die Ausführungsplanung – ist der Schritt, in dem all die genannten Anforderungen in konkrete Planunterlagen und Vorgaben für die Bauausführung übersetzt werden. Gemäß HOAI umfasst LPh 5 das Erarbeiten der vollständigen, ausführungsreifen Planung mit allen Detailangaben, Zeichnungen und technischen Unterlagen. Dies schließt die Koordination sämtlicher Fachplanungen ein (Architektur, Tragwerk, TGA, etc.) und die Integration aller fachspezifischen Anforderungen in ein konsistentes Planwerk.
Für Fertigungsstätten bedeutet das: Jede funktionale Anforderung muss in den Ausführungsplänen eindeutig verortet und beschrieben sein. So sollten beispielsweise alle Übergabepunkte zwischen Gebäudeinfrastruktur und Produktionstechnik klar in den Plänen gekennzeichnet sein – etwa eine Zeichnung, die zeigt, wo die bauseitige Druckluftleitung endet und die Maschinenanschlussleitung beginnt, oder wo der Verantwortungsbereich des Hallen-Elektrikers aufhört und jener des Maschinenlieferanten anfängt. Ein Schnittstellenplan mit Verantwortlichkeitsmatrix ist ein empfohlenes Instrument. Darin werden alle Schnittstellen (Medien, Steuerungen, Konstruktion) aufgeführt und jeweils ein Verantwortlicher (z. B. „bis Kupplung X: Bau, ab dort: Maschinenlieferant Y“) benannt. In der Praxis kann dies im Laufe der Planung als Tabelle oder als gekennzeichnete Zeichnung entstehen.
Weiterhin muss die Ausführungsplanung sicherstellen, dass Wartungs- und Serviceaspekte nicht vergessen gehen: Serviceflächen, Wartungsstege, bewegliche Einbauten etc. sollten in den Plänen und Baubeschreibungen auftauchen. Beispielsweise könnte in einem Detailplan stehen: „Maschine A mit einem Mindestabstand von 1,5 m zur Wand aufstellen, um Zugang für Wartung zu gewährleisten.“ Auch Zeiten für Wartung und Produktionsruhe können in Verträgen und Planungsdokumenten festgehalten werden (z. B. “Wartungsfenster: freitags 14–18 Uhr – Anschlüsse so vorsehen, dass Absperrung in diesem Zeitraum möglich”).
Die Dokumentation spielt eine große Rolle: Ausführungsunterlagen sollten so strukturiert sein, dass sie später ins Facility-Management-System (CAFM) und in die digitale Dokumentation übernommen werden können. Das heißt, Räume und Anlagen sind konsistent zu bezeichnen (Raumbücher, Anlagenkennzeichnungen nach DIN 276 oder VDI 3814) und entsprechende Daten zu pflegen. Beispielsweise kann man in der Ausführungsplanung jedem Wartungsrelevanten Bauteil eine Kennung geben, die im digitalen Wartungsplan auftaucht. Dies erleichtert dem Betreiber die Überführung in den Betrieb deutlich.
Sicherheitsaspekte sollten integraler Bestandteil der Ausführungspläne sein: Brandschutzkonzept, Flucht- und Rettungspläne, Zugangsberechtigungen zu verschiedenen Hallenbereichen usw. sind festzuhalten. In Zeichnungen können z. B. Sicherheitszonen (Bereiche mit PSA-Pflicht, Ex-Schutzzonen nach ATEX) farblich hervorgehoben werden. Die Ausführungsplanung sollte auch sicherstellen, dass bauliche und technische Schutzmaßnahmen (Not-Aus-Schalter, Schutzzäune, Trittroste) an den richtigen Positionen vorgesehen sind. Die Gebäudeautomation (GA) ist ebenfalls frühzeitig mit zu planen: Wenn z. B. Produktionsanlagen mit der Gebäudeleittechnik kommunizieren sollen (etwa zur Lüftungssteuerung nach Maschinenwärme), müssen entsprechende Datenschnittstellen und ein abgestimmtes GA-Konzept in LPh 5 erarbeitet werden. Auch hier hilft ein Rollenkonzept: Welche Datenpunkte liefert der Maschinenbauer, welche der GA-Planer? Und wie werden Zugriffsrechte geregelt (z. B. damit ein Anlagenwart nicht versehentlich gebäudetechnische Systeme lahmlegt).
Wesentlich ist die enge Zusammenarbeit aller Beteiligten in dieser Phase. Insbesondere an der Schnittstelle Fertigung–Facility Management sollten regelmäßig Abstimmungen stattfinden. Ideal ist ein planungsbegleitendes FM (bFM): Ein Vertreter des späteren Betriebs begleitet den Planungsprozess, bringt Praxisanforderungen ein und prüft die Planergebnisse auf Tauglichkeit. So können Planungsfehler proaktiv vermieden werden. Die Ausführungsplanung fungiert hier als Koordinationsplattform: Sie sammelt die Beiträge der Tragwerksplaner (z. B. Fundamentpläne für Maschinen), der TGA-Planer (z. B. Rohrleitungs- und Elektropläne) und der Produktionsplaner (Maschinenaufstellungspläne) und führt sie zu einem stimmigen Gesamtplan zusammen. In einigen Fällen erstellt der Objektplaner (Architekt) auch 3D-Modelle oder BIM-Modelle, um Kollisionen frühzeitig zu erkennen.
Ein oft übersehener Teil ist das Prüfen von Montage- und Werkstattplänen: Gemäß HOAI gehört es zu LPh 5, die Pläne der ausführenden Unternehmen auf Übereinstimmung mit der Planung zu prüfen. Das ist z. B. relevant, wenn ein Anlagenbauer seine eigenen Aufstellungspläne liefert – der Planer sollte kontrollieren, ob diese z. B. die Wartungswege freilassen, die der Gebäudeplan vorsah. Diese Qualitätssicherung verhindert, dass vor Ort plötzlich Abweichungen entstehen, die dem Konzept widersprechen.
Integration bedeutet in LPh 5: Alle zuvor beschriebenen Anforderungen – von Normerfüllung über Infrastrukturdetails bis hin zu Wartungs- und Sicherheitsbelangen – müssen zeichnerisch und textlich in den Planungsunterlagen festgehalten sein. Die Ausführungsplanung für einen Industriebau ist deshalb besonders aufwändig und erfordert Erfahrung in der Industrieplanung. Doch der Aufwand zahlt sich aus: Eine durchdachte Planung reduziert spätere Stillstandszeiten, ermöglicht reproduzierbare Abläufe und gewährleistet einen sicheren Betrieb.
Typische Planungsfehler und Maßnahmen zur Qualitätssicherung
Trotz bester Absichten unterlaufen bei der Planung von Fertigungsstätten immer wieder Fehler, die später zu Problemen führen. Im Folgenden werden einige typische Planungsfehler skizziert und Maßnahmen zur Qualitätssicherung beschrieben, um ihnen entgegenzuwirken.
Häufige Planungsfehler:
Unzureichende Medienkoordination: Wenn z. B. der Spitzenverbrauch von Druckluft oder Strom nicht richtig abgeschätzt wird, kann es zu Medienkonflikten kommen – etwa Druckabfall in der Druckluftversorgung, wenn mehrere Maschinen gleichzeitig hohe Luftmengen ziehen. Fehlende Abstimmung zwischen Produktionsplanung und TGA führt hier zu Engpässen, die im Betrieb Stillstände oder Qualitätsprobleme verursachen können.
Fehlende Wartungszugänglichkeit: Einer der klassischsten Fehler ist es, im Planungsprozess Wartungsflächen zu vernachlässigen. Das Ergebnis können Technikräume sein, die so vollgestellt sind, dass Anlagenkomponenten nicht erreichbar sind, oder Schaltschränke, deren Türen sich an der Wand nicht vollständig öffnen lassen. Auch vorkommend: Revisionsklappen werden in Zeichnungen vergessen, sodass wichtige Hohlräume nachher nicht inspiziert werden können. Solche Versäumnisse erschweren die Instandhaltung enorm.
Störungen der Fertigung durch Instandhaltung: Wurde kein Konzept für Wartungszeiten entwickelt, müssen unter Umständen Wartungsarbeiten im laufenden Betrieb erfolgen – ohne Berücksichtigung des Produktionstakts. So kann es passieren, dass Techniker zur Hauptproduktionszeit eine Anlage abschalten müssen, weil kein alternatives Zeitfenster vorgesehen wurde. Das führt zu Konflikten zwischen Betrieb und Instandhaltung.
Nachrüstbedarf durch fehlende Reserven: Ist die Anlage starr auf den aktuellen Bedarf ausgelegt ohne Reserven (z. B. kein Platz auf Kabelbahnen, keine freien Felder in Verteilerschränken, keine bauliche Erweiterungsmöglichkeit), werden bei der ersten Änderung teure Umbaumaßnahmen fällig. Etwa muss eine Betonsohle aufgegraben werden, um eine zusätzliche Leitung zu verlegen, weil keine Leerrohre vorgesehen waren.
Sicherheitsdefizite: Fehler in der Layoutplanung können dazu führen, dass Sicherheitswege oder PSA-Zonen unberücksichtigt bleiben. Ein typisches Beispiel: Fluchtwege oder Zugänge für die Feuerwehr sind verstellt, weil sie im Plan nicht eindeutig festgelegt wurden. Oder PSA-Wege (Wege, auf denen spezieller Körperschutz zu tragen ist) kreuzen sich ungewollt mit Besucherwegen. Auch kann fehlende Kennzeichnung bzw. Beschilderung auf mangelhafte Planung zurückzuführen sein. Sicherheitslücken dieser Art fallen mitunter erst bei einer Begehung kurz vor Inbetriebnahme auf – dann sind nur noch provisorische Lösungen möglich.
Qualitätssicherung und Gegenmaßnahmen: Um solche Fehler zu vermeiden, ist eine systematische Qualitätssicherung während der Planung entscheidend. Dazu zählen:
Frühe Einbindung erfahrener Praktiker: Wie bereits erwähnt, verbessert die Beteiligung des Facility Managements oder erfahrener Instandhalter in der Planungsphase die Ergebnisqualität enorm. Diese Experten können Planungsentwürfe aus Sicht des späteren Betriebs bewerten und auf Wartungsprobleme oder ineffiziente Lösungen hinweisen. Workshops zwischen Planern und Betrieb (Nutzerabstimmung) sorgen dafür, dass die Planung praxistauglich bleibt.
Checklisten und strukturierte Planungsdurchgänge: Eine bewährte Methode der Qualitätssicherung ist der Einsatz von Checklisten (wie der im Folgenden aufgeführten). Für jede Planungsphase bzw. jedes Gewerk sollte es Prüflisten geben, die der verantwortliche Planer abarbeitet. In LPh 5 kann dies beispielsweise eine Liste sein: „Sind alle Wartungsöffnungen eingeplant?“, „Entsprechen alle Verkehrswege den ASR-Breiten?“, „Wurden Reserven für Erweiterungen berücksichtigt?“ etc. Solche Listen zwingen zu einer systematischen Durchsicht der Planung und reduzieren die Gefahr, wichtige Punkte zu übersehen.
Planungsübergreifende Koordinationstreffen: Regelmäßige Koordinationsbesprechungen zwischen den Fachplanern (Architekt, TGA-Ingenieur, Tragwerksplaner, Produktionsplaner) stellen sicher, dass alle vom selben Stand ausgehen. Hier können Schnitte und Überschneidungen geprüft werden: Passt die Lüftungstrasse zur Maschinenaufstellung? Sind alle Lasten an den richtigen Stellen in der Statik berücksichtigt? Diese Treffen sollten im Plan verankert und dokumentiert sein.
Interne und externe Plausibilitätsprüfungen: Manche Unternehmen ziehen in kritischen Phasen einen externe Peer-Review hinzu – also erfahrene Kollegen oder spezialisierte Prüfer, die die Planung auf Herz und Nieren prüfen. Ebenso sollte der Generalplaner intern eine Plausibilitätskontrolle vornehmen: z. B. einen „Planlauf“ simulieren, in dem er sich vorstellt, den fertigen Betrieb zu betreiben, um Fehler zu entdecken. Moderne Methode ist auch das BIM-Kollisionschecking: ein gemeinsames 3D-Modell kann automatisch auf Kollisionen von Bauteilen prüfen.
Fortschreibung und Kontrolle der Ausführungsplanung: Qualitätssicherung endet nicht mit Fertigstellung der Pläne. Während der Bauausführung müssen Änderungen am Plan, sog. „Fortschreibungen“, kontinuierlich geprüft werden. Der Architekt/Planer sollte Bauleitern und ausführenden Firmen Rückfragen ermöglichen und proaktiv auf Unklarheiten reagieren. Auch die Prüfung von Montageplänen der Firmen (z. B. Werkstattzeichnungen für Stahlbau, Installationspläne für Maschinen) gehört dazu. Diese Verantwortung sollte ernst genommen werden, da Ausführende manchmal aus Kostengründen Vereinfachungen vornehmen wollen, die dem Planungskonzept widersprechen (etwa Weglassen von Wartungsstegen). Hier ist der Planer in der Pflicht, auf Einhaltung der Qualität zu pochen.
Abnahmebegehungen und Tests: Zum Abschluss der Bauarbeiten sollten Begehungen mit allen Beteiligten stattfinden, um die Umsetzung der Planungsanforderungen zu überprüfen. Idealerweise wird ein Probebetrieb (Inbetriebnahme) durchgeführt, bei dem man die Produktionsanlage im Zusammenspiel mit der Gebäudetechnik testet. Frühzeitige Integrationstests – z. B. ob die Lüftung ausreichend Luft liefert, ob Beleuchtungsstärken erreicht werden, ob Alarmanlagen im Lärm gehört werden – geben Gelegenheit, letzte Mängel zu korrigieren, bevor der Regelbetrieb startet. Diese finale Qualitätssicherung kann in LPh 8/9 verortet sein, sollte aber gedanklich schon in LPh 5 vorbereitet werden (durch Festlegen von Testkriterien, Prüfszenarien etc.).
Qualitätssicherung ist also ein laufender Prozess, der in der Planungsphase ansetzt und bis zur Übergabe andauert. Mit strukturierten Prüfungen, enger Zusammenarbeit und dem Blick fürs Detail lassen sich die häufigsten Fehler vermeiden. Letztlich gilt: Eine Fertigungsstätte in der Ausführungsplanung optimal durchzudenken, zahlt sich in ihrem gesamten Lebenszyklus aus – durch geringere Betriebskosten, höhere Sicherheit und Flexibilität sowie einen störungsarmen Produktionsablauf.
Checkliste zur Prüfung der Ausführungsplanung (HOAI LPh 5) – Fertigungsstätten
Kategorie: Gesetzliche/normative Grundlagen | Erfüllt? (Ja/Nein) |
Wurden alle einschlägigen Gesetze und Verordnungen berücksichtigt (ArbStättV, Landesbauordnung, ggf. BImSchG/TA Lärm bei Emissionen)? | |
Sind die Technischen Regeln für Arbeitsstätten (ASR) relevant für das Projekt bekannt und umgesetzt (ASR A1.2 Raumabmessungen, A1.3 Sicherheitskennzeichnung, A1.8 Verkehrswege, A3.4 Beleuchtung, A3.5 Raumtemperatur, A3.6 Lüftung, A3.7 Lärm etc.)? | |
Entsprechen die geplanten Raumhöhen den Vorgaben (lichte Höhe ≥ 2,75 m bei >50 m² Raumgröße gem. ASR A1.2) und den funktionalen Erfordernissen (z. B. Kranbahnhöhe)? | |
Sind die Anforderungen aus DIN-Normen eingehalten (z. B. DIN 18202 Ebenheitstoleranzen für Böden, DIN EN 12464-1 Beleuchtungsstärken, DIN 18041 Raumakustik)? | |
Liegen Nachweise/ Konzepte für besondere Bereiche vor (z. B. Reinraumklasse nach ISO 14644 mit entsprechendem Lüftungskonzept, Ex-Schutz-Zonen Einteilung nach ATEX)? |
Kategorie: Technische Infrastruktur (Versorgung/Entsorgung) | Erfüllt? (Ja/Nein) |
Stromversorgung: Ist die Leistung ausreichend dimensioniert für alle Maschinen und Anlagen (inkl. Reservekapazität für zukünftige Erweiterungen)? | |
Sind separate Stromkreise/Schaltkreise für Produktionsanlagen und Gebäudetechnik vorgesehen (zur Vermeidung von gegenseitiger Beeinflussung)? | |
Wurde ein Notstrom- oder USV-Konzept geprüft (z. B. für IT, Notbeleuchtung, sicherheitsrelevante Systeme)? | |
Druckluft: Ist die Druckluftversorgung mit ausreichender Kompressorleistung, Aufbereitung (Trockner/Filter) und Speichervolumen geplant? | |
Sind eindeutige Schnittstellen für Druckluft definiert (Hauptleitung bauseits bis Anschlusspunkt, Kupplungen zu Maschinen)? | |
Wasser: Ist die Trink-, Brauch- und Kühlwasserversorgung sichergestellt (Druck, Menge, ggf. Rückkühlwerk)? | |
Sind erforderliche Wasseraufbereitungs- oder -sicherheitseinrichtungen vorgesehen (z. B. Enthärtung, Druckerhöhungsanlage, Rohrtrenner/Rückflussverhinderer)? | |
Entsorgung: Gibt es geeignete Einrichtungen für Abwasser (z. B. Ölabscheider, Neutralisationsanlage bei chemischen Abwässern)? | |
Sind ausreichende Entsorgungsflächen und -wege für Abfälle innerhalb und außerhalb der Halle vorgesehen (Müllsammelstellen, Containerstellplätze, Zufahrt für Entsorger)? | |
IT/Netzwerk: Ist ein strukturiertes Datennetz geplant (ausreichende Anzahl Datenanschlüsse an Arbeitsplätzen/Maschinen, WLAN-Abdeckung, industrielle Bussysteme falls nötig)? | |
Wurden Redundanz und IT-Sicherheit bedacht (z. B. Doppelverlegung kritischer Datenleitungen, getrennte Netze für Office und Produktion)? | |
Sind alle notwendigen Medien (Strom, Daten, Druckluft, technische Gase etc.) in ausreichender Anzahl und an den richtigen Positionen an den Maschinen eingeplant? |
Kategorie: Gebäude und Layout (Raum, Boden, Konstruktion) | Erfüllt? (Ja/Nein) |
Raumaufteilung: Entspricht die Anordnung der Funktionsbereiche (Produktion, Lager, Technikräume, Sozialbereiche) dem Nutzungsbedarf und wurden Pufferflächen berücksichtigt? | |
Bodenlasten: Ist die Tragfähigkeit der Bodenplatte für alle geplanten Lasten nachgewiesen (Maschinenfundamente, Regallasten, Verkehrslasten)? | |
Sind ggf. separate Maschinenfundamente oder Schwingungsisolierungen für erschütterungserzeugende Maschinen vorgesehen? | |
Bodenebenheit: Wurden Ebenheitsanforderungen an den Boden definiert (z. B. DIN 18202 Toleranzklasse, besonders glatt für Fördertechnik/Flurförderzeuge)? | |
Bodenbelag: Ist ein zum Prozess passender Belag vorgesehen (rutschhemmend, staubbindend, ableitfähig für ESD-Schutz, chemikalienbeständig etc.)? | |
Wände/Decken: Sind Oberflächenmaterialien gewählt, die den Anforderungen genügen (Schallschutz, Reinigungsfreundlichkeit, ggf. Brandschutzanforderungen)? | |
Baukonstruktion: Sind ausreichend Montageöffnungen oder Aussparungen in Wänden/Decken für die Installation von Technik (Leitungsdurchführungen, Klappen) eingeplant? | |
Wurden eventuell benötigte Kräne oder Hebezeuge in die Planung integriert (Tragkonstruktion für Kranbahn, Befestigungspunkte in Decke etc.)? | |
Ist die Gebäudeaussteifung und -statik auf mögliche spätere Anbauten oder Aufstockungen vorbereitet (z. B. Fundamentverstärkungen, Anschlussstellen)? |
Kategorie: interne Verkehrs- und Logistikflächen | Erfüllt? (Ja/Nein) |
Fußwege: Sind gehbereich für Mitarbeiter klar definiert und markiert? Entsprechen ihre Breiten der ASR A1.8 (≥ 0,9 m bzw. ≥ 1,2 m je nach Personenzahl)? | |
Fahrzeugwege: Sind Fahrwege für Stapler oder Routenzüge geplant? Haben diese ausreichend Breite (Fahrzeugbreite + 2×0,5 m Sicherheitsabstand) und Wendeflächen? | |
Gibt es Trennungen oder Barrieren zwischen Fußgänger- und Fahrzeugverkehr (Geländer, Markierungen, Ampelsysteme an Kreuzungen)? | |
Türen/Tore: Sind Türen und Tore an sinnvollen Positionen für Verkehrsflüsse platziert und ausreichend dimensioniert (Torbreite/Höhe für Transportgüter, Schnelllauftore für Frequenz)? | |
Flucht- und Rettungswege: Entsprechen die Fluchtwege den Anforderungen (Mindestbreiten, maximale Fluchtweglängen)? Sind Notausgänge in ausreichender Zahl und gut erreichbar vorhanden? | |
Lagerflächen: Sind ausreichende interne Lager- und Pufferzonen vorgesehen (inkl. Verkehrswege in Lagerbereichen, z. B. Gänge zwischen Regalen gemäß BG-Vorgaben)? | |
Anlieferung/Versand: Sind Laderampen, Andockstellen und Verkehrswege für LKW geplant, inkl. Rangierflächen und ggf. Warteflächen? | |
Handhabung von Material: Wurden für schwere oder sperrige Bauteile innerbetriebliche Transportmittel eingeplant (z. B. Hallenkran, Hebebühnen, Rollenbahnen)? | |
Verkehrswege in Technikräumen: Sind auch für Instandhalter in den Technikzentralen ausreichende Bewegungsflächen und Zugänge (Gänge ≥ 0,6 m, Türhöhe ≥ 1,95 m) vorgesehen? |
Kategorie: Arbeitsumgebung (Licht, Klima, Schall, Luft) | Erfüllt? (Ja/Nein) |
Beleuchtung: Wird die ASR A3.4 „Beleuchtung“ eingehalten (Tageslichtnutzung maximal, künstliche Beleuchtung mit erforderlichen Lux-Werten für alle Arbeitsplätze)? | |
Sind blendfreie Leuchten und eine gleichmäßige Ausleuchtung vorgesehen (Bereiche ohne störende Schlagschatten, keine Direktblendung durch Sonne oder Leuchten)? | |
Gibt es ein Konzept für Sicherheitsbeleuchtung (Notbeleuchtung bei Stromausfall, beleuchtete Fluchtwege, gemäß ASR A3.4/7)? | |
Raumtemperatur: Sind Heizung/Kühlung so ausgelegt, dass die Mindesttemperaturen nach ASR A3.5 eingehalten werden (+20 °C leicht, +17 °C mittel, +12 °C schwer) und übermäßige Sommerhitze vermieden wird? | |
Ist die Art der Beheizung angemessen (z. B. Strahlungsheizung für Hallen, um Zugluft zu minimieren)? Wurden Wärmeschutzmaßnahmen gegen sommerliche Überhitzung getroffen (Dämmung, Lüftung, baulicher Sonnenschutz)? | |
Lüftung: Ist ein Lüftungskonzept vorhanden, das ausreichende Frischluftversorgung sicherstellt (freie Lüftung oder RLT-Anlage mit Berechnung der erforderlichen Luftmengen gemäß ASR A3.6)? | |
Werden Luftschadstoffe oder Wärme aus Prozessen gezielt abgesaugt (Punktabsaugungen, Quelllüftung in heißen Bereichen)? | |
Ist die Lüftungsanlage auf zuverlässigen Dauerbetrieb ausgelegt und sind Maßnahmen bei Ausfall definiert (Alarmierung, Ersatzlüftung)? | |
Lärm: Wird der Lärmpegel an Arbeitsplätzen minimiert (laute Maschinen gekapselt oder in schallgedämmte Räume verlegt)? Liegt eine Prognose/ Berechnung der zu erwartenden Lärmbelastung vor? | |
Sind Schallschutzmaßnahmen geplant (Absorber an Decke/Wand, schwingungsentkoppelte Aufstellung von Anlagen, leise Ventilatoren etc.)? | |
Wurden Kommunikationsbereiche identifiziert, die besonderen Schallschutz brauchen (z. B. Leitstände, Büros in der Produktion) und entsprechend ausgeführt (z. B. Kabinen mit Schalldämmung)? | |
Erfüllt das Konzept die Vorgaben der LärmVibrationsArbSchV (Auslösewerte 80/85 dB(A)) bzw. sind Bereiche >85 dB(A) als Gehörschutzbereiche eingeplant und gekennzeichnet? | |
Besondere Klima/Hygiene: Falls Reinräume, Kühlräume oder besonders staubarme Bereiche geplant sind – wurden hierfür alle speziellen Anforderungen berücksichtigt (Überdruckhaltung, Filter, Schleusen, Materialien etc.)? |
Kategorie: Instandhaltung und Reinigung | Erfüllt? (Ja/Nein) |
Wartungsflächen: Sind vor allen wartungspflichtigen Anlagen ausreichend Freiflächen eingeplant (z. B. vor Schaltschränken ≥ 1,2 m, um Kessel, Lüftungsgeräte etc.)? | |
Sind Wartungspunkte zugänglich (Filter, Ventile, Messgeräte über Leitern/Podeste erreichbar; Revisionsklappen an allen erforderlichen Stellen vorhanden)? | |
Gibt es einen zentralen Zugang zu Dach- und Deckentechnik (Gesicherte Steigleiter, Dachausstieg, Laufsteg zu Lüftungsgeräten etc.)? | |
Ist die Zerlegbarkeit/Demontage von Anlagen für Wartungszwecke bedacht (z. B. ausreichend Raum, um einen Motor herauszuziehen oder ein Ventilatorrad zu wechseln)? | |
Wurden mögliche Wartungszeiten bzw. -fenster mitgeplant (z. B. Drosselstrecken, Absperrschieber, Bypassleitungen, um Wartung im Teilbetrieb zu ermöglichen)? | |
Dokumentation: Werden alle relevanten Anlagen mit Kennzeichnungen versehen, die in ein Wartungs-/CAFM-System überführt werden können (Anlagenkennzeichnung im Plan)? | |
Reinigungskonzept: Sind die Oberflächen und Bauweisen auf gute Reinigbarkeit ausgelegt (glatte, robuste Oberflächen, keine Schmutznischen)? | |
Sind ggf. Reinigungszonen im Layout erkennbar (Schmutzschleusen, getrennte Rein- und Schmutzbereiche, z. B. Schwarz/Weiss-Bereiche)? | |
Gibt es ausreichende Bodeneinläufe/Gullys an sinnvollen Stellen für Nassreinigung oder bei möglichen Flüssigkeitsaustritten? | |
Sind Wand- und Deckenflächen zugänglich genug gehalten, um sie reinigen zu können (z. B. Zwischendecken mit begehbaren Bereichen oder abnehmbare Verkleidungen)? | |
Wurden in der Planung Räume oder Plätze für Reinigungsequipment vorgesehen (Putzmittelräume, Ladestationen für Putzmaschinen etc.)? | |
Entsorgung von Produktionsrückständen: Falls besondere Rückstände anfallen (Späne, Stäube, Abwasser), sind hierfür Entsorgungseinrichtungen und Reinigungsintervalle vorgesehen? |
Kategorie: Flexibilität und Zukunftsvorsorge | Erfüllt? (Ja/Nein) |
Erweiterungsflächen: Gibt es am Gebäude oder Grundstück Reserven für mögliche Erweiterungsbauten (und sind dafür bereits Vorkehrungen getroffen, z. B. Fugen, Brandschutzkonzepte, statische Vorbereitungen)? | |
Modulare Bauweise: Sind nicht tragende Trennwände/Einrichtungen möglichst modular ausgeführt, so dass Umbauten vereinfacht werden (z. B. Systemtrennwände, Stecksysteme)? | |
Medienreserven: Sind Leerrohre, Reservekabel, Anschlussreserven (zusätzliche Abzweige mit Blindflanschen) für zukünftig weitere Medien oder Geräte eingeplant? | |
Skalierbarkeit: Lassen sich zusätzliche Maschinen in den Layout integrieren, ohne komplette Neuorganisation (z. B. durch von vornherein definierte Aufstellungsflächen oder Erweiterungsmodule)? | |
Flexibilität in Gebäudetechnik: Ist die HLK-Anlage so dimensioniert, dass moderate Laststeigerungen (z. B. +10–20%) aufgefangen werden könnten? Sind Erweiterungsmöglichkeiten vorgesehen (Platz für weitere Lüftungsgeräte, Reserveleistung Kälteerzeuger etc.)? |
Kategorie: Planungsdokumentation und Qualitätssicherung | Erfüllt? (Ja/Nein) |
Schnittstellenabstimmung: Liegt ein Plan/Übersicht aller Schnittstellen zwischen Bau und Produktion vor (inkl. Verantwortlichen für jede Schnittstelle)? | |
Sind alle Auflagen aus behördlichen Genehmigungen in der Ausführungsplanung berücksichtigt (z. B. Brandschutzauflagen, Immissionsschutz, Arbeitsschutzforderungen aus Genehmigungsbescheiden)? | |
Wurden alle Gewerke in den Plänen koordiniert (Kollisionsplanung: passen Tragwerk, Maschinen, Lüftung, Elektroführungen übereinander)? | |
Sind die Pläne ausreichend detailliert (z. B. im Maßstab 1:50 oder größer für kritische Bereiche, Details 1:10) und enthalten sie alle benötigten Angaben für die Ausführung? | |
Wurde ein Prüfprozess implementiert (z. B. Planprüfliste oder 4-Augen-Prinzip intern) um die Pläne vor Freigabe zu kontrollieren? | |
Haben alle relevanten Beteiligten die Planung geprüft und freigegeben (Bauherrenvertretung, Nutzer/Fertigungsverantwortliche, Sicherheitsfachkraft, Facility Management)? | |
Wird die Ausführungsplanung fortgeschrieben und aktualisiert bei Änderungen während der Bauausführung (Change Management, Planindex)? | |
Ist sichergestellt, dass Montage- und Werkstattpläne der ausführenden Firmen vom Planer geprüft werden (Übereinstimmung mit Planung, keine unautorisierten Änderungen)? | |
Wurden alle Qualitätskontrollen und Abnahmen, die in LPh 8/9 stattfinden müssen, bereits vorbereitet (Definition von Prüfkriterien, z. B. Abgabetests für Anlagen, Check der Beleuchtungsstärken, Messung der Luftmengen etc.)? | |
Ist die Dokumentation für den späteren Betrieb vorgesehen (Bedienungsanleitungen, Prüfprotokolle, Wartungspläne als Bestandteil der Abschlussdokumentation)? |